Dr. Mobin Rahman, ChemOne's VP for Technology, at Asian Downstream Summit 2024
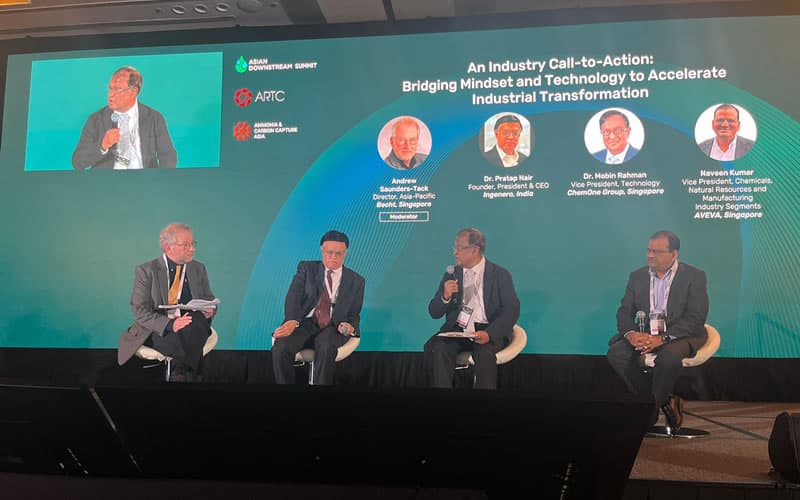
30 October 2024
In October 2024, Dr. Mobin Rahman, ChemOne’s Vice President for Technology, participated as a featured speaker for a panel discussion at the Asian Downstream Summit titled ‘An industry call-to-action: Bridging mindset and technology to accelerate industrial transformation’, alongside other participants from Becht Engineering, Ingenero Technologies, and AVEVA.
The future of petrochemicals
Petrochemicals are deeply embedded in modern life, forming the backbone of countless products we rely on daily. This includes plastics, fertilisers, packaging, clothing, digital devices, medical equipment, detergents, tires and more.
A McKinsey report from 2022 estimates that the global petrochemical industry will continue to grow at a rate of three percent per year in the next decade – largely driven by strong demand for plastics and rapid economic development across markets such as China, India, and Southeast Asia.
Despite how heavily dependent modern economies are on petrochemicals, it remains one of the key blind spots in our global energy transition, particularly given its strong influence on future energy trends.
The importance of refineries in the energy transition
The drive for sustainability and climate awareness is revolutionising the chemical industry. Project operators may choose to leverage the following innovative solutions and/or technologies to reduce carbon emissions across their existing refineries or plants
- Feedstock alternatives
There is potential for petrochemical plants to transition to renewable feedstocks, such as biomass from sugar-yielding plants or wood biomass, to reduce reliance on fossil fuels.
- Process technology configuration changes
As the demand for fossil fuel is expected to decrease overtime, forward looking refineries may look to leverage crude oil-to-chemicals (COTC) technologies, merging the production of petrochemicals into a traditional refinery to build one integrated processing plant.
This helps them to create higher-value chemicals from lower value oil, improve cost effectiveness of their operations by maximising profit derived from a set amount of crude oil, and extend their value creation opportunities by tapping into the growing chemicals market demand.
- Decarbonisation pathways to a greener refinery
Process electrification, in other words, using low-carbon electricity to meet process energy needs traditionally met with fossil fuels – is an effective solution for reducing a refinery’s carbon emissions. This also allows refineries to incorporate more renewable energy into their energy mix, for example, from solar, wind, or biogas.
Alternatively, using wind or solar-powered electrolysis to produce “green” hydrogen can further help to decarbonise industrial processes.
- Digitalisation and increased automation
At ChemOne, our key philosophy is that the simplest and most straightforward emissions reduction is via efficiency. Plants that integrate new digital processes and automation into their design are more efficient, cost less, and produce less chemical waste. This then helps to reduce carbon emissions overall and create a more sustainable operation.
If we take ChemOne’s Pengerang Energy Complex, for example, the incorporation of Honeywell UOP’s LD Parex technology is expected to result in reduced energy consumption, maximised aromatics production, lowered capital costs alongside wider feedstock flexibility, effectively allowing the PEC plant to become one of the most advanced, energy and carbon efficient facilities in its class.
In summary, the refineries of tomorrow will remain competitive and resilient via strong margins and a low carbon intensity. According to Dr. Mobin, achieving this will require a strong combination of a mindset shift across the industry alongside a willingness to innovate and continuously improve – underpinned by relevant policy initiatives, for example, the European Green Deal and the US’s Inflation Reduction Act, to further drive the energy transition.